Team:Cornell/Construction
From 2011.igem.org
DanVLevine (Talk | contribs) |
|||
Line 116: | Line 116: | ||
Models</span></li> | Models</span></li> | ||
<ol type="i" style="margin-left: 0.375in; direction: ltr; unicode-bidi: embed; margin-top: 0in; margin-bottom: 0in; font-family: 'Comic Sans MS'; font-size: 10pt; font-style: normal; "> | <ol type="i" style="margin-left: 0.375in; direction: ltr; unicode-bidi: embed; margin-top: 0in; margin-bottom: 0in; font-family: 'Comic Sans MS'; font-size: 10pt; font-style: normal; "> | ||
- | <li value="1" style="margin-top:0;margin-bottom:0;vertical-align:middle"><span style="font-style: normal; font-family: 'Comic Sans MS'; font-size: 10pt; "> | + | <li value="1" style="margin-top:0;margin-bottom:0;vertical-align:middle"><span style="font-style: normal; font-family: 'Comic Sans MS'; font-size: 10pt; ">Streptavidin</span></li> |
- | + | ||
<li style="margin-top:0;margin-bottom:0;vertical-align:middle"><span style="font-family:"Comic Sans MS";font-size:10.0pt">VioE</span></li> | <li style="margin-top:0;margin-bottom:0;vertical-align:middle"><span style="font-family:"Comic Sans MS";font-size:10.0pt">VioE</span></li> | ||
</ol> | </ol> | ||
Line 134: | Line 133: | ||
<p style="margin:0in;margin-left:.375in;font-family:"Comic Sans MS";font-size: | <p style="margin:0in;margin-left:.375in;font-family:"Comic Sans MS";font-size: | ||
- | 10.0pt"><span style="font-weight:bold">Component Development | + | 10.0pt"><span style="font-weight:bold">Summary of Component Development:</span></p> |
<ol type="1" style="margin-left: 0.75in; direction: ltr; unicode-bidi: embed; margin-top: 0in; margin-bottom: 0in; font-family: 'Comic Sans MS'; font-size: 10pt; font-style: normal; "> | <ol type="1" style="margin-left: 0.75in; direction: ltr; unicode-bidi: embed; margin-top: 0in; margin-bottom: 0in; font-family: 'Comic Sans MS'; font-size: 10pt; font-style: normal; "> | ||
Line 154: | Line 153: | ||
Chip Model - Modeled in Solidworks. Cleaned up mesh in Modo. Textured in | Chip Model - Modeled in Solidworks. Cleaned up mesh in Modo. Textured in | ||
Modo.</span></li> | Modo.</span></li> | ||
- | <li style="margin-top:0;margin-bottom:0;vertical-align:middle"><span style="font-family:"Comic Sans MS";font-size:10.0pt"> | + | <li style="margin-top:0;margin-bottom:0;vertical-align:middle"><span style="font-family:"Comic Sans MS";font-size:10.0pt">Streptavidin - Point |
data found using PDB databases. Polycount reduced and protein refined in | data found using PDB databases. Polycount reduced and protein refined in | ||
Blender.<span> </span>Imported to and textured | Blender.<span> </span>Imported to and textured | ||
Line 164: | Line 163: | ||
<ol type="i" style="margin-left: 0.375in; direction: ltr; unicode-bidi: embed; margin-top: 0in; margin-bottom: 0in; font-family: 'Comic Sans MS'; font-size: 10pt; font-style: normal; "> | <ol type="i" style="margin-left: 0.375in; direction: ltr; unicode-bidi: embed; margin-top: 0in; margin-bottom: 0in; font-family: 'Comic Sans MS'; font-size: 10pt; font-style: normal; "> | ||
<li value="1" style="margin-top:0;margin-bottom:0;vertical-align:middle"><span style="font-style: normal; font-family: 'Comic Sans MS'; font-size: 10pt; ">Experimented | <li value="1" style="margin-top:0;margin-bottom:0;vertical-align:middle"><span style="font-style: normal; font-family: 'Comic Sans MS'; font-size: 10pt; ">Experimented | ||
- | with recoil dynamics package. In tests, seemed feasible. However,<span> </span>given high resolution of protein | + | with recoil dynamics package. In tests, this seemed feasible. However,<span> </span>given the high resolution of protein |
- | models, very difficult to implement with given resources.</span></li> | + | models, it would be very difficult to implement with given resources.</span></li> |
</ol> | </ol> | ||
<ol type="i" style="margin-left: 0.375in; direction: ltr; unicode-bidi: embed; margin-top: 0in; margin-bottom: 0in; font-family: 'Comic Sans MS'; font-size: 10pt; font-style: normal; "> | <ol type="i" style="margin-left: 0.375in; direction: ltr; unicode-bidi: embed; margin-top: 0in; margin-bottom: 0in; font-family: 'Comic Sans MS'; font-size: 10pt; font-style: normal; "> | ||
- | <li value="2" style="margin-top:0;margin-bottom:0;vertical-align:middle"><span style="font-style: normal; font-family: 'Comic Sans MS'; font-size: 10pt; ">Developed | + | <li value="2" style="margin-top:0;margin-bottom:0;vertical-align:middle"><span style="font-style: normal; font-family: 'Comic Sans MS'; font-size: 10pt; ">Developed flow system |
as part of an animation rig. Rig contained functions that would output | as part of an animation rig. Rig contained functions that would output | ||
varying degrees of morph-mapped position deformations in relation to the | varying degrees of morph-mapped position deformations in relation to the | ||
- | distance of a protein from its target bond-site. In practice, didn't look | + | distance of a protein from its target bond-site. In practice, this didn't look |
- | as nice as intended. Also very processor intensive | + | as nice as intended. Also very processor intensive: caused Modo to become |
- | very unstable. Abandoned this element of the rig. </span></li> | + | very unstable. Abandoned this element of the rig due to these setbacks. </span></li> |
<li style="margin-top:0;margin-bottom:0;vertical-align:middle"><span style="font-family:"Comic Sans MS";font-size:10.0pt">Went back to recoil | <li style="margin-top:0;margin-bottom:0;vertical-align:middle"><span style="font-family:"Comic Sans MS";font-size:10.0pt">Went back to recoil | ||
dynamics package. Reduced resource drain of proteins using a manually | dynamics package. Reduced resource drain of proteins using a manually | ||
- | modeled protein with significantly | + | modeled protein with significantly fewer polygons. Had proteins follow an |
attractive force constrained via path constraint to a curve running along | attractive force constrained via path constraint to a curve running along | ||
- | the tube. Simulation and efforts successful - satisfactory flow achieved | + | the tube. Simulation and efforts successful - satisfactory flow was achieved |
for 140 globular style proteins. Future updates may increase number or | for 140 globular style proteins. Future updates may increase number or | ||
improve flow behavior.</span></li> | improve flow behavior.</span></li> | ||
Line 186: | Line 185: | ||
<ol type="1" style="margin-left: 0.75in; direction: ltr; unicode-bidi: embed; margin-top: 0in; margin-bottom: 0in; font-family: 'Comic Sans MS'; font-size: 10pt; font-style: normal; "> | <ol type="1" style="margin-left: 0.75in; direction: ltr; unicode-bidi: embed; margin-top: 0in; margin-bottom: 0in; font-family: 'Comic Sans MS'; font-size: 10pt; font-style: normal; "> | ||
<li value="8" style="margin-top:0;margin-bottom:0;vertical-align:middle"><span style="font-style: normal; font-family: 'Comic Sans MS'; font-size: 10pt; ">Coating | <li value="8" style="margin-top:0;margin-bottom:0;vertical-align:middle"><span style="font-style: normal; font-family: 'Comic Sans MS'; font-size: 10pt; ">Coating | ||
- | Channels with | + | Channels with Streptavidin:</span></li> |
<ol type="i" style="margin-left: 0.375in; direction: ltr; unicode-bidi: embed; margin-top: 0in; margin-bottom: 0in; font-family: 'Comic Sans MS'; font-size: 10pt; font-style: normal; "> | <ol type="i" style="margin-left: 0.375in; direction: ltr; unicode-bidi: embed; margin-top: 0in; margin-bottom: 0in; font-family: 'Comic Sans MS'; font-size: 10pt; font-style: normal; "> | ||
<li value="1" style="margin-top:0;margin-bottom:0;vertical-align:middle"><span style="font-style: normal; font-family: 'Comic Sans MS'; font-size: 10pt; ">Created a | <li value="1" style="margin-top:0;margin-bottom:0;vertical-align:middle"><span style="font-style: normal; font-family: 'Comic Sans MS'; font-size: 10pt; ">Created a | ||
- | mesh skin from chip model surface | + | mesh skin from chip model surface and replicated streptavidin proteins onto |
- | surface. | + | surface. Main roadblock encountered was in problems with overlapping.</span></li> |
</ol> | </ol> | ||
<ol type="i" style="margin-left: 0.375in; direction: ltr; unicode-bidi: embed; margin-top: 0in; margin-bottom: 0in; font-family: 'Comic Sans MS'; font-size: 10pt; font-style: normal; "> | <ol type="i" style="margin-left: 0.375in; direction: ltr; unicode-bidi: embed; margin-top: 0in; margin-bottom: 0in; font-family: 'Comic Sans MS'; font-size: 10pt; font-style: normal; "> | ||
<li value="2" style="margin-top:0;margin-bottom:0;vertical-align:middle"><span style="font-style: normal; font-family: 'Comic Sans MS'; font-size: 10pt; ">New mesh | <li value="2" style="margin-top:0;margin-bottom:0;vertical-align:middle"><span style="font-style: normal; font-family: 'Comic Sans MS'; font-size: 10pt; ">New mesh | ||
- | skin created from chip model surface | + | skin created from chip model surface, incorporating offsets from channel edges. Replication of proteins using replicators was |
successful. Attempted replicator freeze to get individual instances for | successful. Attempted replicator freeze to get individual instances for | ||
recoil dynamics (</span><span style="font-style: italic; font-family: 'Comic Sans MS'; font-size: 10pt; ">see system for bonding</span><span style="font-style: normal; font-family: 'Comic Sans MS'; font-size: 10pt; ">). | recoil dynamics (</span><span style="font-style: italic; font-family: 'Comic Sans MS'; font-size: 10pt; ">see system for bonding</span><span style="font-style: normal; font-family: 'Comic Sans MS'; font-size: 10pt; ">). | ||
- | Proteins too complex for given resources | + | Proteins too complex for given resources, making freeze scene unusable.</span></li> |
<li style="margin-top:0;margin-bottom:0;vertical-align:middle"><span style="font-family:"Comic Sans MS";font-size:10.0pt">Using developed | <li style="margin-top:0;margin-bottom:0;vertical-align:middle"><span style="font-family:"Comic Sans MS";font-size:10.0pt">Using developed | ||
animation rig, instanced rig. Manually placed rig instances on channel | animation rig, instanced rig. Manually placed rig instances on channel |
Revision as of 23:17, 28 September 2011
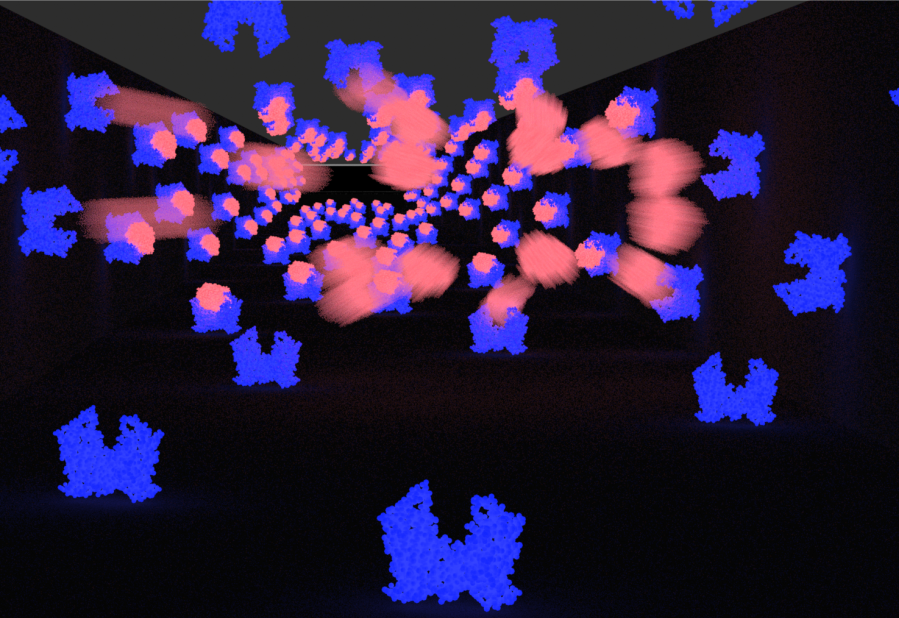
Original Description
- Lysate gunk is flowed down the tube
- As lysate flows enzymes are attracted to surface (strept surface)
- words "Now Device Constructed"
Interpreted Components:
- Macroscale Environment
- Syringe Pump Model
- Syringe Model
- Tube Model
- Microfluidic Chip Model
- Biological Models
- Streptavidin
- VioE
- System for Flow
- System for Channel Coating
- System for Bonding
Summary of Component Development:
- Syringe Model - Measured Dimensions in Lab. Modeled and textured scale model in Modo.
- Syringe Pump Model - Used online dimensions for syringe pump used in lab. Modeled and textured in modo.
- Tube Model - Measured Dimensions in Lab. Modeled and textured in Modo.
- Microfluidic Chip Model - Modeled in Solidworks. Cleaned up mesh in Modo. Textured in Modo.
- Streptavidin - Point data found using PDB databases. Polycount reduced and protein refined in Blender. Imported to and textured in Modo.
- VioE - Point data found using PDB databases. Polycount reduced and protein refined in Blender. Imported to and textured in Modo.
- System for Flow:
- Experimented with recoil dynamics package. In tests, this seemed feasible. However, given the high resolution of protein models, it would be very difficult to implement with given resources.
- Developed flow system as part of an animation rig. Rig contained functions that would output varying degrees of morph-mapped position deformations in relation to the distance of a protein from its target bond-site. In practice, this didn't look as nice as intended. Also very processor intensive: caused Modo to become very unstable. Abandoned this element of the rig due to these setbacks.
- Went back to recoil dynamics package. Reduced resource drain of proteins using a manually modeled protein with significantly fewer polygons. Had proteins follow an attractive force constrained via path constraint to a curve running along the tube. Simulation and efforts successful - satisfactory flow was achieved for 140 globular style proteins. Future updates may increase number or improve flow behavior.
- Coating Channels with Streptavidin:
- Created a mesh skin from chip model surface and replicated streptavidin proteins onto surface. Main roadblock encountered was in problems with overlapping.
- New mesh skin created from chip model surface, incorporating offsets from channel edges. Replication of proteins using replicators was successful. Attempted replicator freeze to get individual instances for recoil dynamics (see system for bonding). Proteins too complex for given resources, making freeze scene unusable.
- Using developed animation rig, instanced rig. Manually placed rig instances on channel surface using quad view and snapping. Successful. Worked for rig.
- Maintaining successful rig scene as an option. Created an jittered instance array of lower resolution avidin meshes for use with reverse dynamic technique (see system for bonding)
- System for Bonding:
- Idea to use dynamics simulation and run in reverse. Attempted with frozen instances of replicated high resolution avidins. Too resource intensive. Unusable.
- Developed animation rig that enabled permanent bonding using distance and angle measurements relative to locaters placed at the starts of channels and across from protein bond target sites. VioE "flowing" proteins parented to a locater constrained to a curve defining the general path of flow. Successful, but not "molecular" looking enough for some team members.
- Reattempt at dynamics using much lower resolution meshes. Somewhat successful, more random and real looking. Less effective at getting the point across. Work in progress.
Modifications to Description:
- In order to simplify things for the audience and the animators, cell gunk was limited to proteins of focus.
- Scene was also divided into separate tube and bonding scenes for simplicity and clarity.
- The tube scene acts as a transition between E. Coli lysis and bonding.
- Bonding scene switches to clear view of channel bonding.
- "Construction" switched to screen output of Syringe Pump to introduce the construction process and help the audience understand what's going on.
Summary of Scene Progression
Preview Draft Bonding Scene
- Animation Rig Assembly - (08/02/2011 - 09/04/2011)
- (08/02/2011 - 08/11/2011)
First Rendition using dot product of position vectors to protein and protein target. Achieved accurate bonding for single protein. Great on test bed, lots of trouble when transplanted to real thing --> couldn't scale up effectively. System scratched.
- (08/18/2011 - 09/04/2011)
From previous system, understood the need to make a test bed significantly more like the scene with the scene scale. System developed described briefly in System for Bonding in Component Development Summary. In summary used and conditions with locaters placed to measure a variety of variables so that once bonding occurred proteins would exhibit no further motion. System was scalable. Replaced stand-in geometry with proper outputs. Rig instanced and placed 140 times for reach instance of bonding. Success. Ran off a single key-framed channel.
- Component Assembly (08/11/2011 - 09/04/2011)
- Before building the new test bed straight into the scene, established the macroscopic scene.
- (08/11/2011 - 08/18/2011)
Scaled up macroscale components to 200,000x their actual size to make things easier to work with. Created basic scene layout.
- (08/18/2011 - 09/04/2011)
Picked and modified texturing to allow for a balance of decent render times and visual appeal.
- Experimental Dynamics Work (09/11/2011 - present)
- (09/11/2011 - present)
Developed low resolution meshes for proteins. Running simulations. Desired results not quite achieved yet.
Reception and Review: Team would like more dynamic work. Otherwise, satisfied with result.
Full Draft Tube Scene (08/1/2011 - 09/11/2011) :
- Dynamics Testing - (08/1/2011-08/11/2011)
Learned how to use dynamics package to achieve a semblance of flow through a tube. Learned the importance of making sure mesh centers are aligned. Also learned how to properly align mesh centers.
- Rigged Motion - (08/02/2011 - 09/04/2011)
Rig did not provide nice enough flow and was barely usable when including morph map system. Scratched.
- Dynamics and new Component Assembly - (09/04/2011 - 09/11/2011)
Used final System for Flow component described in Component Development. 140 globular style proteins with dynamics. Baked movements. Did a lot of camera work with targets, graph editor, and path constraints to achieve desired result.
Reception and Review: Very positive feedback.